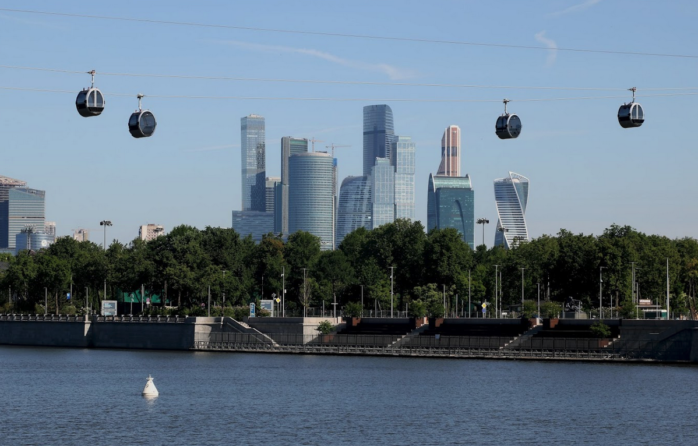
Cities, SI Urban 2/2021, Tourism
Bartholet – Fewer Downtimes thanks to optimal maintenance
Cable cars are one of the world’s most reliable modes of transport. Among other things, this is due to the constant improvements made on these high-performance systems. Gondolas, stations and maintenance systems: nothing is taken for granted and the result is constant improvement.
One company that is heavily involved with the development of better systems is Swiss cable car manufacturer BARTHOLET. The traditional company has a wealth of experience with the cable-drawn transport systems and therefore knows which aspects are critical, especially in the urban setting.
At the BARTHOLET Academy, the individual tasks at the respective stations are covered comprehensively. The tools required for this can be found directly at the respective station.
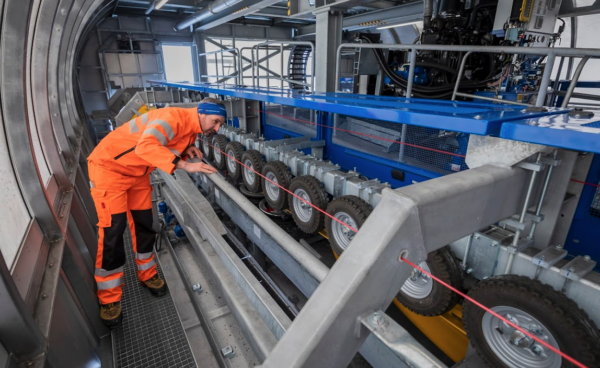
Availability
For local public transport, the issues of reliability and availability are always important. Passengers need to have confidence in a transport system, in order to build it into their daily routine. Continuous operation generates all- important passenger confidence, but what is the best way to achieve this?
One option is to avoid downtimes. Long maintenance times are therefore impossible in urban areas. With regular inspections and maintenance work, faults are automatically minimised and it is therefore ensured that a system is used to optimal capacity.
In addition, there are various helpful developments that can further reduce the maintenance times of a cable car, for example such as automatic, multi- point lubrication.
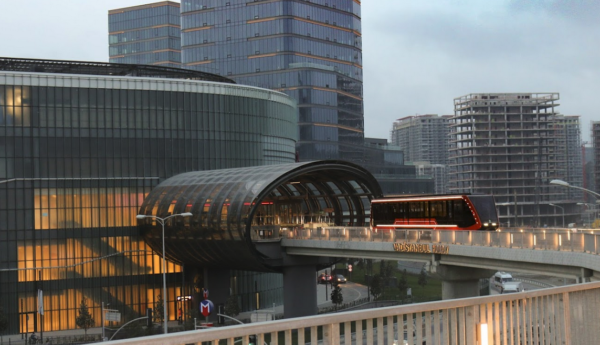
Lubrication on point
One key aspect in the maintenance of an urban cable car is lubrication of the central bearings. To this end, multi-point lubrication is a unique development from BARTHOLET, which significantly reduces inspection and maintenance work.
The positioning of the lubrication points means that optimal lubrication is achieved both in the bearing positions and in the intermediate spaces. It is therefore impossible for moisture to get into the surroundings of the bolt.
Corrosion becomes a thing of the past. In development, durability was not the only key factor; optimal accessibility for maintenance was also important. To this end, the lubrication points were positioned so that more space remains available for the required work.
The Line Monitor, the smart cable sheave from BARTHOLET, works independently. It is fitted respectively at the start and end of the sheave assembly and it measures relevant data. The cable sheave is fitted in such a way that no cabling is needed.
The energy required on the sensors can be produced by the sheave itself. Data are transmitted via radio from the sheave to the repeater on the support head and onwards from one support to the next, until the nearest station.
There, the measured values are displayed and archived on the computer. As well as this, there are many other developments from the Swiss manufacture, which aid the smooth operation of an urban cable car.
For perfect training of cable car staff on the respective system, BARTHOLET has set up a special training centre at its head office in Flums. The primary aim of the academy is straightforward knowledge transfer and the sharing of knowledge about the function and use of all critical cable car components.
Cable car systems have already been used successfully for a number of years in Brest (France) and Moscow (Russia), and users in Vadistanbul (TURKEY) also rely on a system from BARTHOLET.
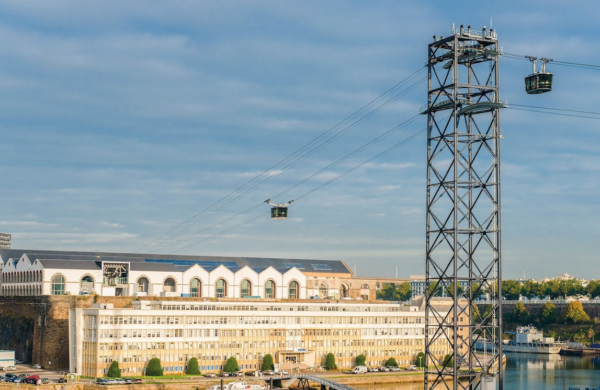