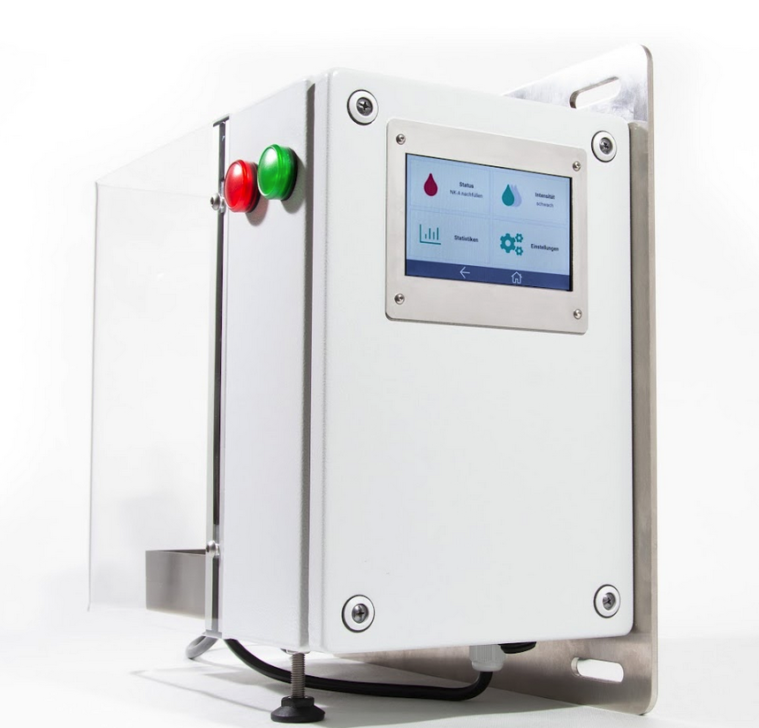
Cities, SI Urban 2/2021, Tourism
Cable oiler – Automatic lubrication for cable car cables
In Pisa too, the road from airport to city centre is one of the routes that is most at risk of congestion. Thanks to the “PisaMover” MiniMetro from LEITNER, this trouble spot has been relieved since 2017, and the journey from Aeroporto Galileo Galilei on the southern edge of Pisa to Stazione Centrale now takes only five minutes.
Each of the two trains comprises three interconnected gondolas and offers spaces for 107 passengers. Around two million passengers use the cableway every year – in all weathers. There is therefore a corresponding strain on the cables.
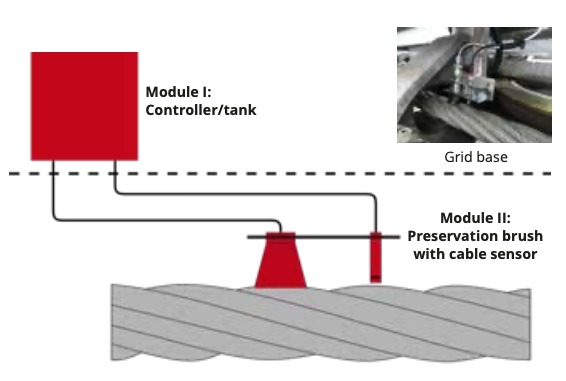
Prolonging the lifetime of the cable
In Pisa, the strain from corrosion was so severe that the cable needed replacing after two rather than four years, Christian Scartezzini from cable car manufacturer LEITNER reports. Its subsidiary, “People Mover Service”, operates and maintains the installation. “To avoid replacing the cable and instead achieve a longer lifetime, we changed the cable model and installed the automatic cable oiler from ELASKON,” Scartezzini says.
Disadvantages of manual lubrication
This decision avoids many disadvantages of manual lubrication, as Sven Winter, CEO of development company ROTEC, emphasises: “Preservation is generally applied manually to cable car cables once or twice per year. To do this, however, the system must be stopped and the weather must be good.”
Also, large quantities of lubricant are used here. These contain solvents, which need to evaporate. With incorrect application, there is a risk of oil dripping onto gondolas or passengers and of roller rubbers wearing more quickly (unevaporated solvents).
Moreover, classic cable preservation is very personnel, time and cost-intensive. “For urban cable car installations, the operators always had to set out at night with the lubricating brush – which is completely impractical,” says Michael Kronschnabl from lubricant manufacturer ELASKON.
Although lubricating devices that are not permanently installed do exist, they are associated with a high application of lubricant and an increased workload.
The cable oiler has improved the avail- ability of the PisaMover. Photo: LEITNER
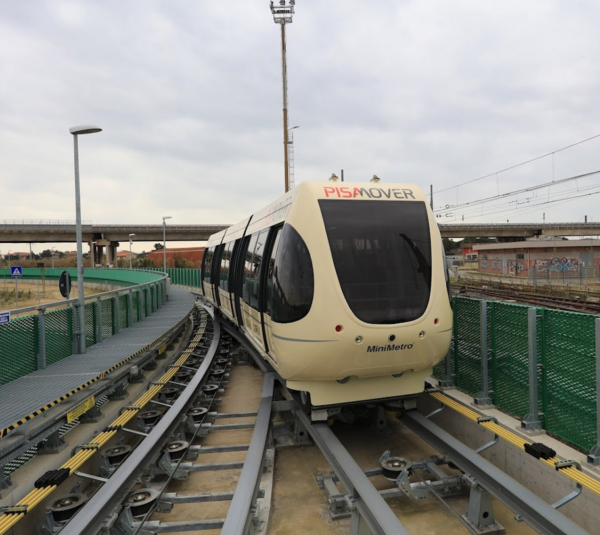
Advantages of the cable oiler
This is why Kronschnabl recommends use of the cable oiler in combination with special oil ELASKON NK-A: “We offer the comprehensive solution of cable oiler and special oil for cable car operators, for automatic preservation in ongoing operation.”
The oil quantity is tailored precisely to the installation; the lubricant consumption is around half as much as with manual lubrication. “With the cable oiler, the cable runs faultlessly and we record far fewer cable fractures under the same load,” Sven Winter adds.
Thanks to the ROTEC software, which calculates the cable volume, the cable oiler always knows how much lubricant to apply. This all-in-one system provides huge relief for operations managers. “The specially developed ELASKON NK-A displays highly stable viscosity, adheres very well to the cable and offers outstanding penetration.”
The result is optimal corrosion protection with no undesirable side-effects (e.g. such as slipping terminals, roller chuck disintegration, dripping and contamination). “We are also happy to look after cable oiler installation and adjustment as well as staff training,” Kronschnabl confirms.
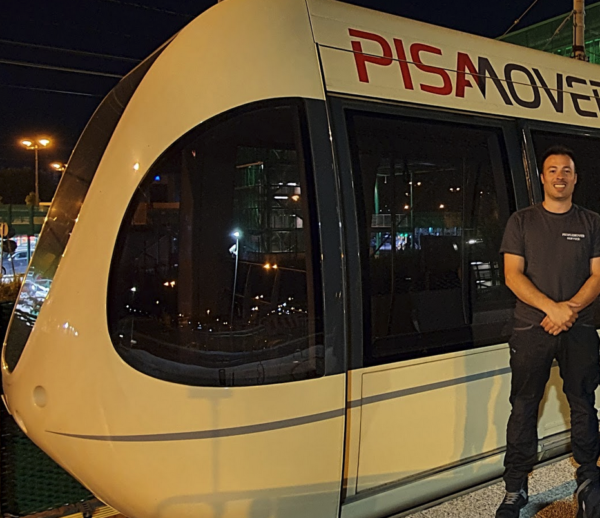
Massimo Ferri, PisaMover operations manager
Massimo Ferri, PisaMover operations manager
“We are very pleased with the cable oiler. The automatic and continuous lubrication saves us from oiling the cable manually, which we would otherwise have to do every 20 days – time that we can now use for other tasks.
Oiling during ongoing operation is very important for availability of the cableway: we operate for 18 hours per day, 365 days per year. Thanks to the statistics, we can also control and adjust the oil consumption. But the most important thing is the extended life of the cable, which we already see since the installation of the automatic cable oiler.
The dream team
The cable oiler consists of two small modules, which can be installed flexibly. MODULE I contains the oil reservoir with a tank volume of 0.7 litres, the controller, and the operating and display elements. It is easy to install on a grid base, on a bracket or on the station wall.
MODULE II is attached directly to the cable. It applies small quantities of oil in a controlled way based on the cable route, monitors the cable speed, and oils the cable car in normal operation. The system is subject to constant further development.
In the latest innovation, the software has been extended to six languages – in addition to German and English, the cable oiler can now also be operated in French, Spanish, Italian and Chinese.
In turn, ELASKON NK-A is a specially developed, solvent-free, transparent oil. It is applied automatically and continuously to the steel cable, in small quantities – tailored precisely to the cable car. This means the cable has enough time to absorb the oil. The coefficients of friction are not significantly reduced and the system remains clean.
Numerous recommendations
“All these advantages mean that we recommend installation of the automatic cable oiler to our customers who operate urban systems,” says Christian Scartezzini from cable car manufacturer LEITNER. The experience in Pisa demonstrates that installation of a cable oiler makes sense not only on new systems but also on existing cableways.
“Cable car association O.I.T.A.F. also recommends its use,” Winter is pleased to report, having developed the product in close cooperation with manufacturers, associations and scientists. Around 30 systems have already been sold worldwide. The aims are always the same: to improve cableway availability and to ease the strain on staff – and to save plenty of money.
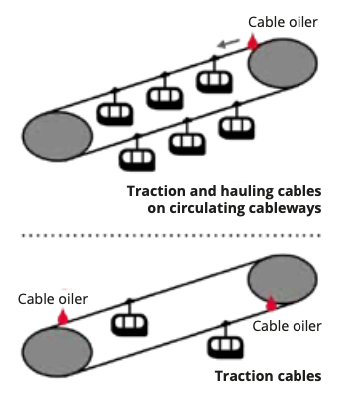