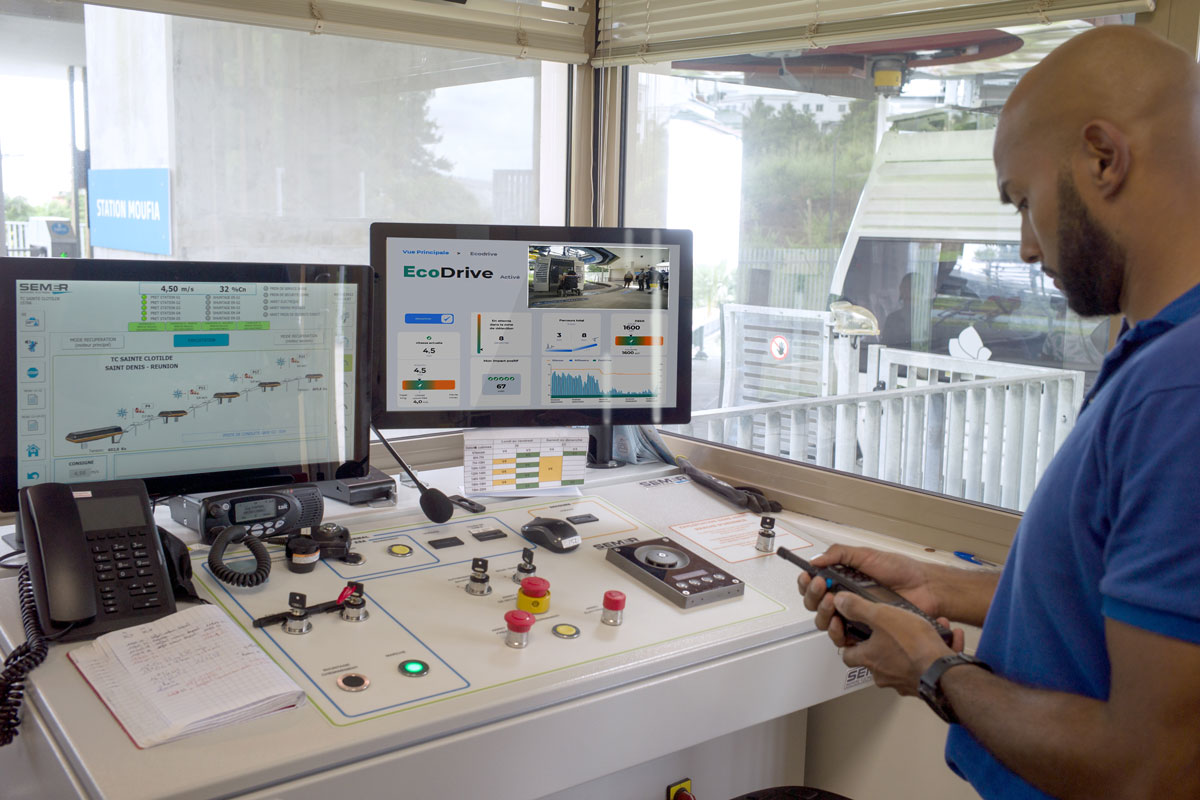
Cities, SI Urban 2/2022
Ecodrive: Sustainable Innovation
With the ECODRIVE, an automatic adaptive speed control for ropeways, up to 20 percent of energy can be saved.
The gearless DirectDrive drivesystem from POMA and LEITNER, which saves up to five percent of energy in comparison with conventional drives and also scores points with high reliability, user-friendliness and ease of maintenance, is still unrivalled on the ropeway market.
A DirectDrive
offers the smoothest possible running, minimal maintenance requirements, sustainable operation and low operating costs.
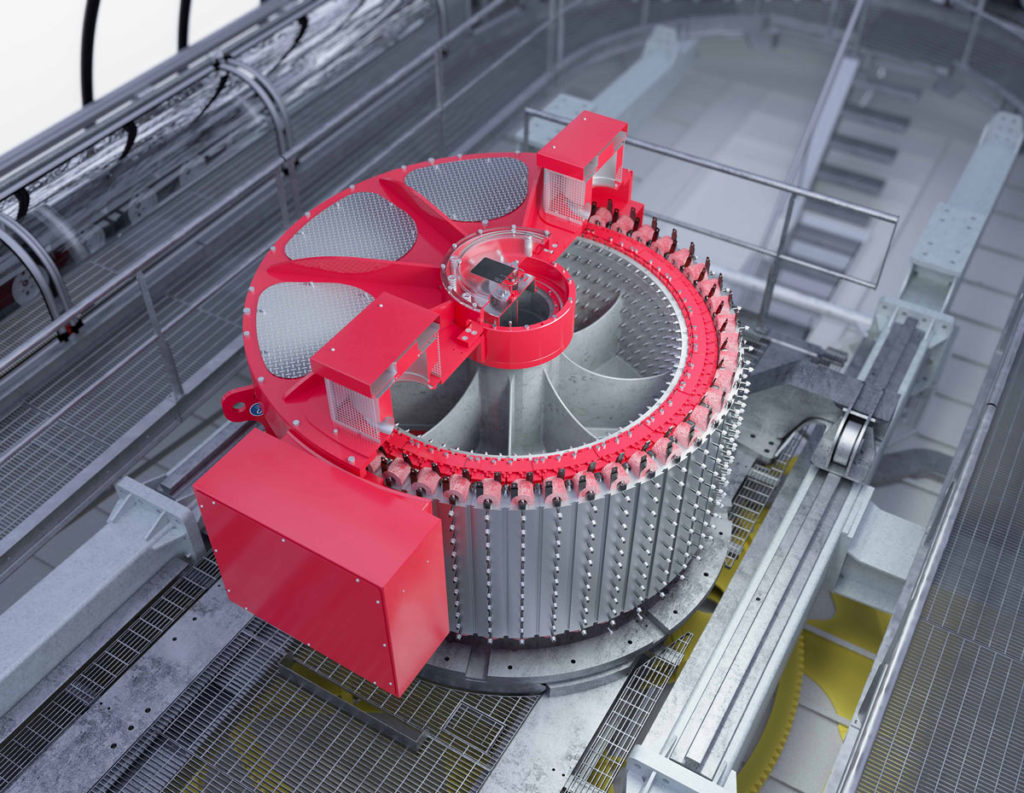
Adaptive speed control
POMA and LEITNER see themselves as innovative and sustainable manufacturers and partners responsible for finding answers to current problems and supporting customers with corresponding product developments.
Especially, in the current, tense situation with regard to energy costs, inflation and scarcity of resources, the manufacturers are also called upon to contribute to relieving the burden in these economically challenging times through applied research and development.
With the ECODRIVE, a system that has already been successfully implemented in seven ropeway systems, POMA and LEITNER meet the requirements for energy-saving technologies.
The adaptive speed control for ropeways is integrated into the control unit and regulates the speed of the ropeway on the basis of a camera system, which records the number of passengers waiting at the stations.
In this way, energy saving of up to 20 percent is possible through automatic speed reduction from 5 m/s to 4 m/s, for example, without the ride comfort being impaired.
Another ecologically and financially relevant effect of the technology developed by POMA and LEITNER is less wear on the material.
With the EcoDrive,
energy-efficient operation of urban ropeways operation is easier to achieve. Photos: POMA/LEITNER
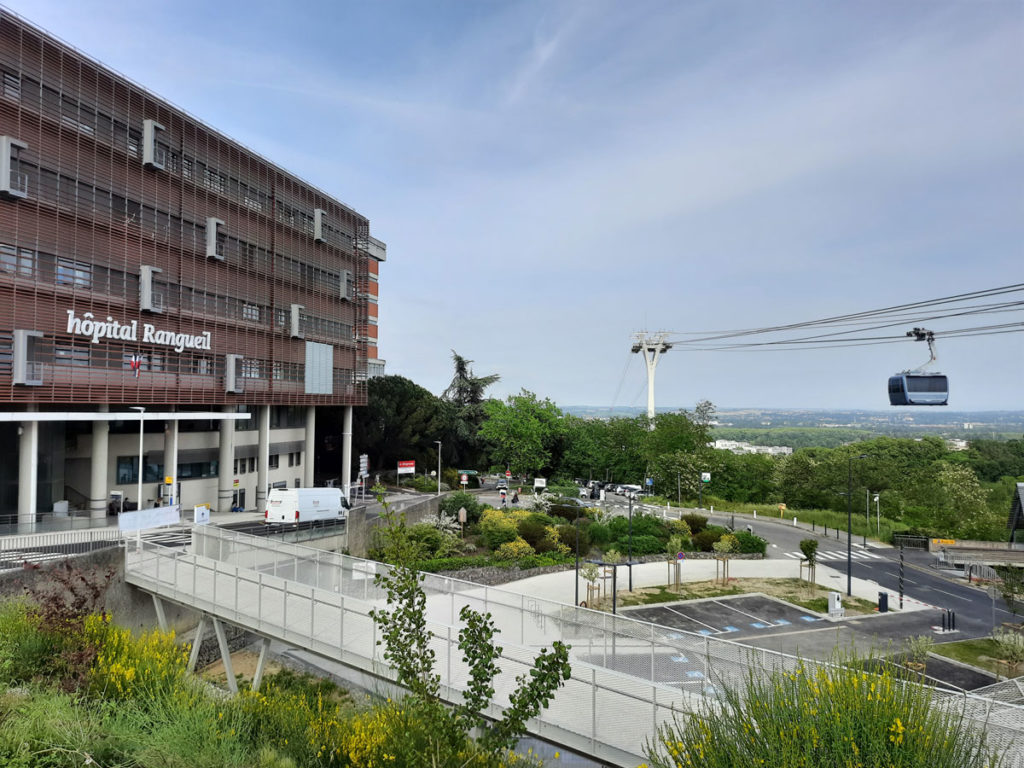
The ECODRIVE, which is available for new installations as well as for retrofitting on existing ropeways, thus also contributes to extension of the service life and creates significant added value in terms of sustainable and resource-saving operation.
An important role in the development of the ECODRIVE is played by POMA subsidiary SEMER, which specialises in the engineering and manufacturing of electrical equipment and industrial automation for ropeway transport systems.
It is recognised worldwide for its know-how in electrical engineering, safety-instrumented systems, process control and industrial automation.
First tests on Alpine ropeways
Initial results are already available from the 2021/22 season in the Serre Chevalier ski resort. The savings potential was measured on two different ropeways respectively on 23 and 21 days of the season, respectively.
The results are impressive: savings of 7,550 kWh and 5,000 kWh were achieved during these time periods. This savings potential is also interesting for urban ropeways, especially since they run significantly more and for longer than classic mountain lines.
Advantage from DirectDrive
Another example of further, ecologically oriented development is gearless drive system “DirectDrive”, which has been in use at POMA and LEITNER for over 20 years and on over 250 ropeways.
This perfected technologyachievesefficiencyofup to 96 percent in the partial to peak load range and is therefore clearly in pole position on the market.
The redundancy of the DirectDrive design also contributes to the optimum performance. The high availability of the system is particularly important for urban ropeways, as numerous people rely on public transport.
A DirectDrive offers the smoothest possible running, minimal maintenance requirements (no transmission overhaul, no transmission oil change), sustainable operation (no oil and lubricants) and unbeatably low operating costs, as it reduces the energy consumption by up to 5 percent in comparison with a conventional drive.