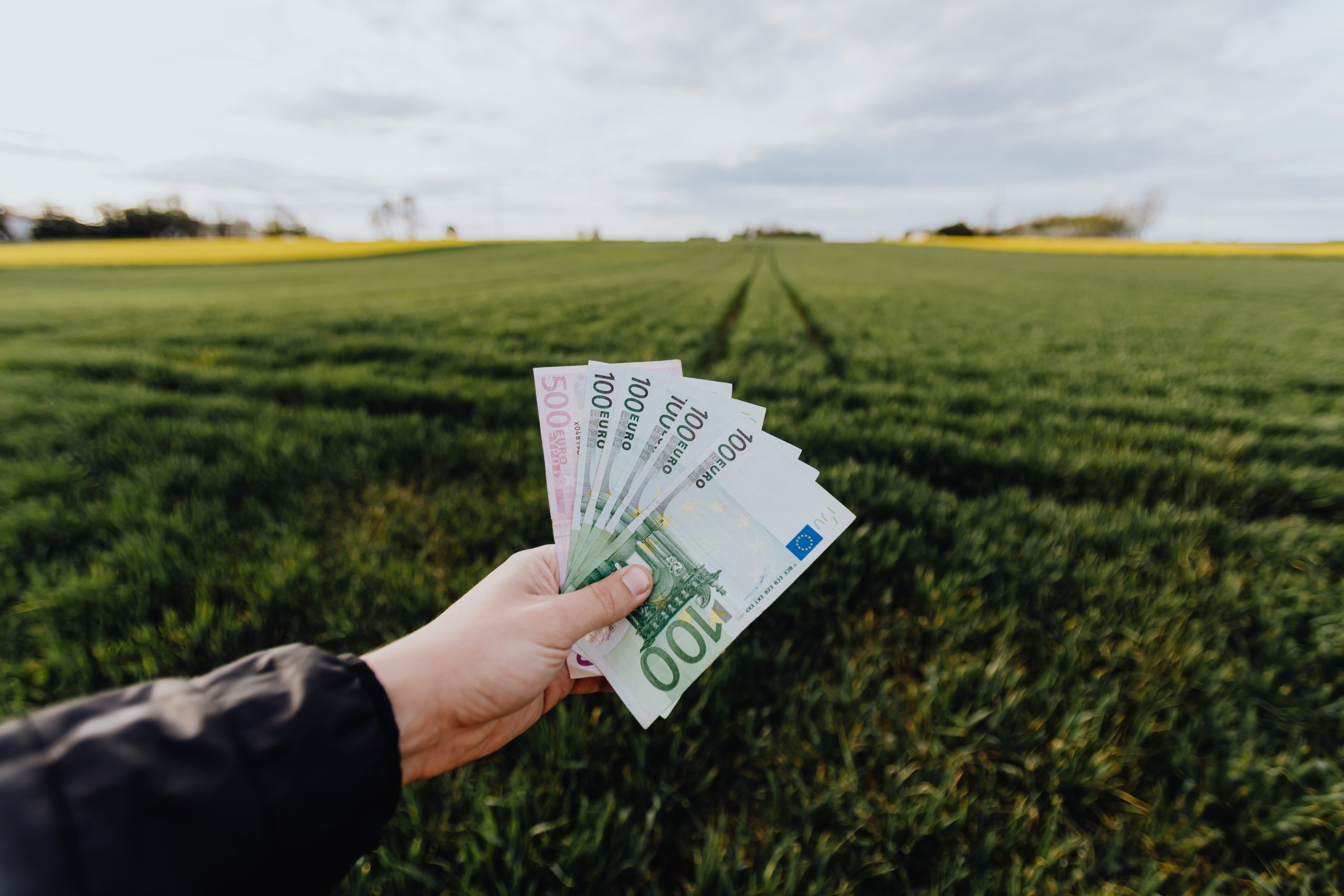
Management & Tourism
Inflation and shortages
Supply shortages
For cable car manufacturer DOPPELMAYR, procurement times have become longer all over the world, and this trend is going to continue. “The shortage of catalogue items and C-parts, especially in the areas of electronics and hydraulics, poses new challenges for us every day,” Production Division Manager Karl-Heinz Zündler reports.
Swiss gear manufacturer KISSLING is likewise affected by supply shortages. “Some lead times are increasing by eight weeks, which is obviously very unsatisfactory for everyone,” Head of Sales and Marketing Roman Siegfried says. Snow cutter manufacturer WESTA is also suffering severely from the present situation. “For some components from Germany and Italy, for which lead times of three to four months were previously normal, we now have to factor in lead times of twelve to 16 months,” Managing Director Alois Weber laments.
In the area of raw material supply, there are shortages at chain manufacturer HANS HALL, especially in key products, which cannot be avoided. “We are talking about 30 to 35 weeks here, just to illustrate the explosiveness of the situation,” Managing Director Hans Hall says. That means materials ordered now will not be available until October/ November.
For control supplier FREY AG Stans, the delivery situation depends on the day. Products with long lead times, such as motors and frequency converters, can generally be obtained in four to five months. “By contrast, smaller parts take longer. Semiconductors already have a lead time of half a year,” Sales & Service Head of Division Ivo Zehnder reports. FREY AG STANS is therefore ordering key components early, at its own risk.
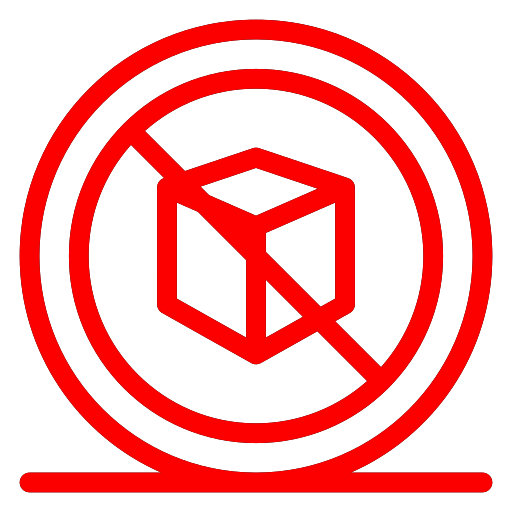
Material costs
Prices of raw materials – especially of steel, copper, aluminium and plastic – have increased sharply since the start of the crisis and there is a basic shortage of raw materials. For the LEITNER group of companies, the situation is having an impact especially in the electronics market.
“Even if you are prepared to pay more for components, some are currently very difficult to obtain,” DEMACLENKO, PRINOTH and LEITNER write in their joint statement.
This assessment is shared by Ivo Zehnder from FREY AG Stans: “Purchasing costs have risen by ten to 15 percent. We worry especially about small components, such as terminals, relays and switches, as these additional costs are difficult to absorb.” On the other hand, KISSLING AG mentions 30 percent higher material costs for its gears.
DOPPELMAYR also reports massive price rises: during the crisis, the price of sheet steel rose by approx. 90 percent and it has currently levelled off at plus 75 percent – with a slight upward trend once again. Aluminium and copper prices have almost doubled. Even plastics are affected by this trend. “In addition, there are price increases in freight and logistics, as well as a shortage of electronic components, which in turn has a negative effect on price,” Karl-Heinz Zündler says.
Huge rises in purchase prices – especially for steel – have also been recorded by snow cutter manufacturer WESTA: “80 percent higher costs will have an impact on our price lists in the spring,” Alois Weber predicts.
Hans Hall makes a similar point: “Material costs have increased by between 15 and 40 percent, and energy prices likewise.”
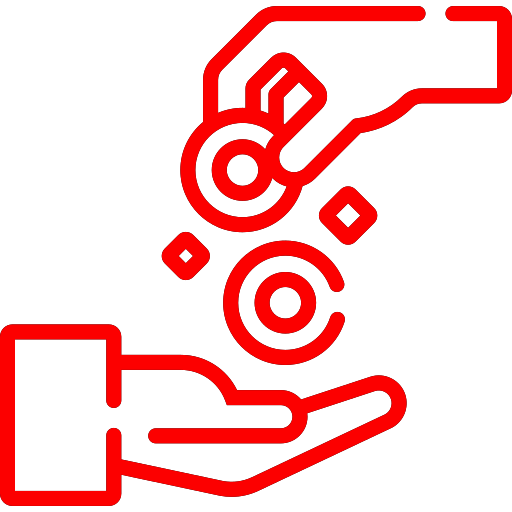
Prices
For eight years, MOUNTAINCART was able to keep its vehicle price constant – through automation, in-house production and process optimisation. “This year, however, we have to raise prices by a moderate eight to nine percent for the first time.
Here, we are passing on only what we have to,” Managing Director Joachim Jeßberger reports. At DOPPELMAYR, higher prices are dependent on the system type, as Karl-Heinz Zündler emphasises: “The higher the proportion of steel and aluminium, the greater the cost increase. However, we are at least in the range of double-digit percentages.”
Buyers of KISSLING gears must temporarily expect to pay four percent more, Roman Siegfried says: “That is a drop in the ocean in view of the increased cost of materials.” Even snow machine manufacturer TECHNOALPIN is expecting increased prices for its products, as a result of the rates for raw materials. FREY AG STANS has difficultly generally with price rises:
“Because the additional costs are difficult to gauge, owing to the volatile supply situation, we can pass on the increases partially for larger components – such as motors, frequency converters and cables – but we continue to monitor the situation in the area of smaller control components and cables.”
Chain manufacturer HANS HALL increased prices already in the 2021/2022 winter season – and is announcing a further rise in the second quarter of 2022. JAKOB ROPE SYSTEMS also introduced two temporary inflation surcharges in the past year, to compensate a little for increased material and transport prices. Editor’s note: The costs for this page have also increased by 26 percent in the last two months!
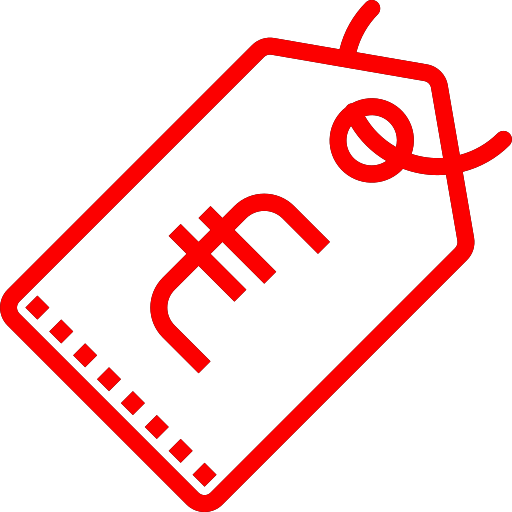