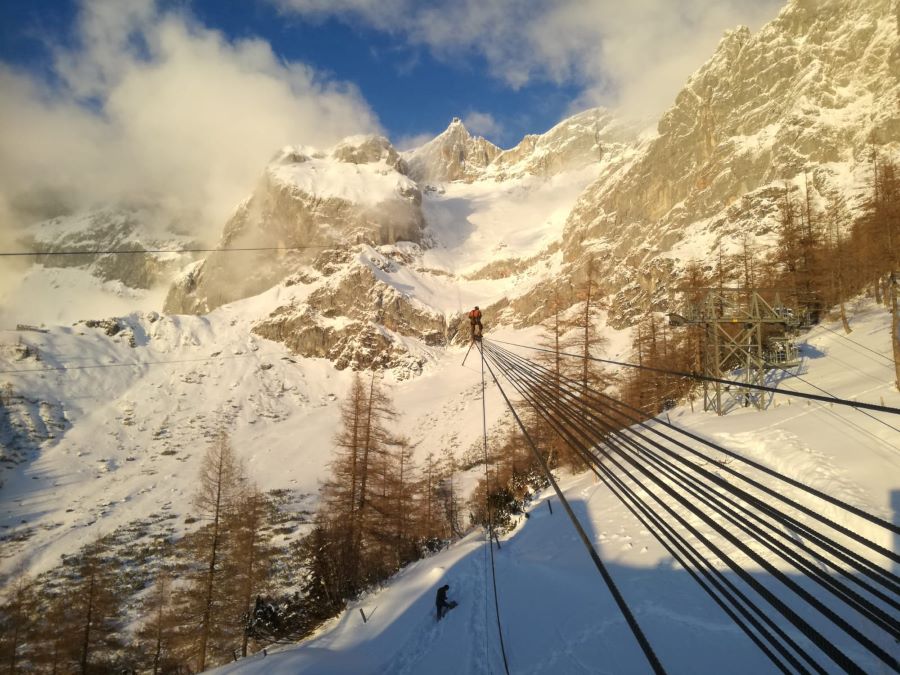
Cableway & Technology
Dieter Röser: The man for the cable
SI: Mr Röser, what does a cable installation involve?
Dieter Röser: Basically it’s no different from fitting a kitchen (he laughs). As a carpenter, I can say that. Generally, our whole team comes from different industries – sometimes unrelated to cable cars. This diversity of knowledge is a major advantage; you learn the elements specific to the cable in practice – not just from training courses.
So experience is crucial?
Yes, in our industry you become a professional only if you have been doing it for many years. I have been on the road for INAUEN-SCHÄTTI since 2007, first as a freelancer and then as an employee, and now actually as head technician. Every day I learn something new, every job is different, every project makes an impact.
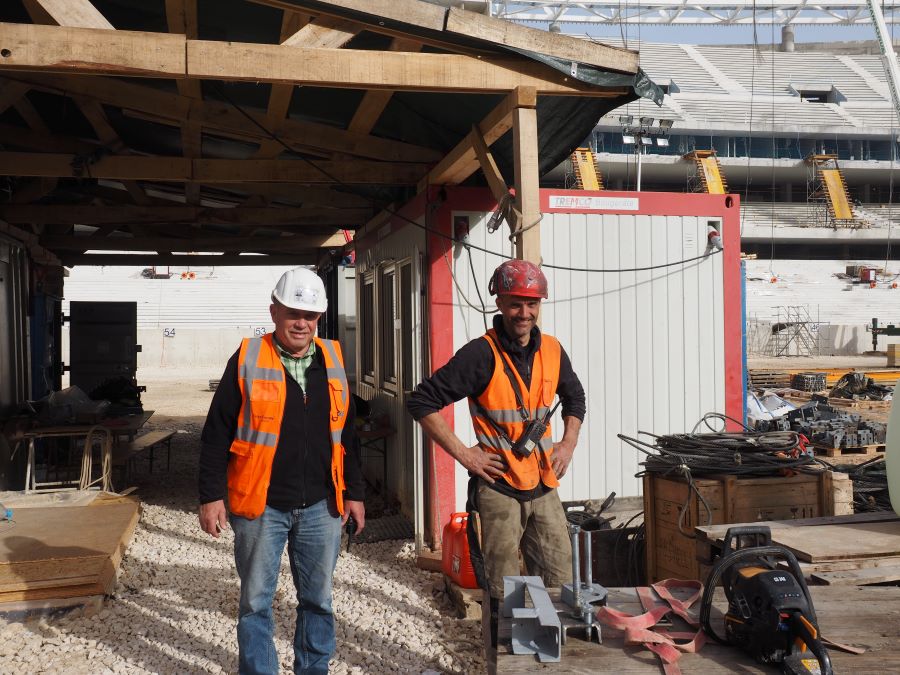
Dieter Röser installing cable roofs at the stadium of Atlético Madrid.
Which installations are the most memorable?
Installing a 60-tonne supporting cable in Andorra was definitely one of my most exciting projects. But the installation of the station roofs in Madrid and Warsaw, and working on the roofs of tram stops in Qatar also made an impression on me. I was working in the Arab country for three months.
So you have to enjoy being away.
If you don’t like travelling, this is definitely the wrong job for you. But I like being on the road: one week on a mountain at 3,000 meters, then the next week in the city – I love the contrast. Most jobs are in Europe but INAUEN-SCHÄTTI does also send me to China occasionally. I get to meet lots of people there, which is nice.
What else do you find exciting in your job?
have drawn over 100 cables, but every order is different. I like the variety and the improvisation. At INAUEN-SCHÄTTI we love anything that falls outside the usual pattern. Specialisms are our speciality.
Dieter Röser’s tasks also include bridge installations, such as here in Ticino.
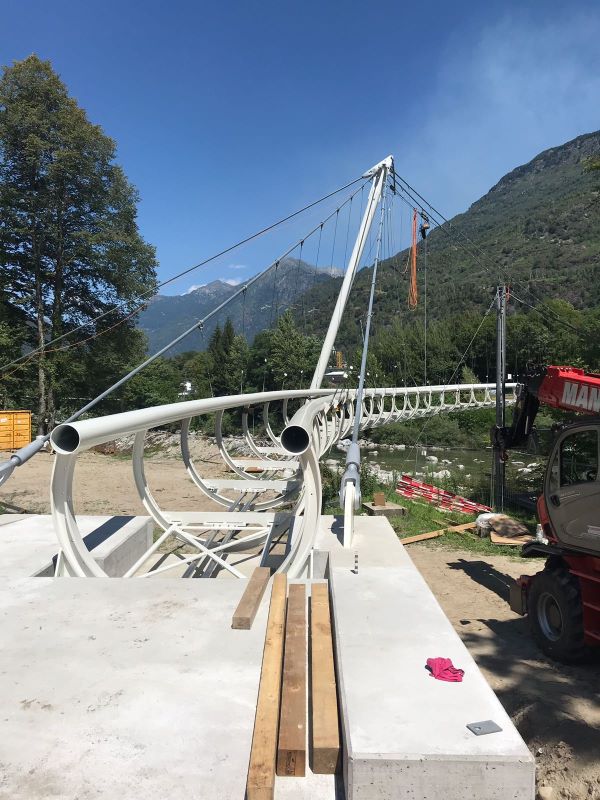
At the same time, the assignment areas are very broad.
Yes, I admit I like the fact that I don’t “just” install cable car cables. INAUEN-SCHÄTTI is very diverse: I build bridges, install roofs, spread cable nets and much more. We do it all – from jetty to chairlift!
What do you not like so much about your work?
Obviously it’s nicer when I get to install new, clean cables, rather than overhauling greasy, old cables. But the exciting technology of the old tracks often makes up for this minor unpleasantness.
And what about the frequently harsh weather?
Cold, wind and snow are no problem: I can prepare for them. As a German, working outside in the mountains is what initially attracted me to Switzerland. Storms there are on a different level, so you have to stop work in good time, as the top priority is for everyone to get home safely.
Dieter Röser hat einen Arbeitsplatz mit Aussicht – wie hier auf der Riederalp.
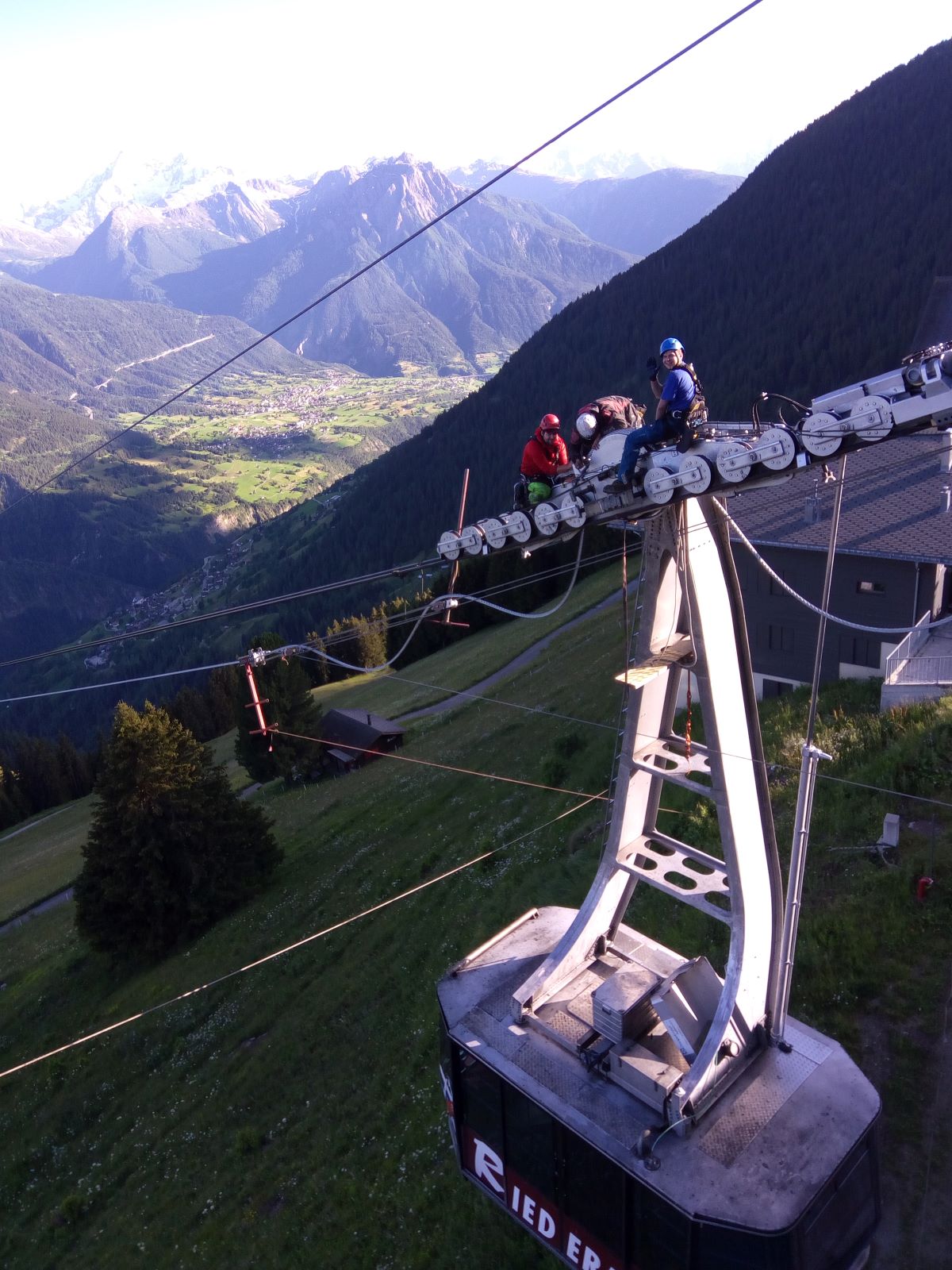
Have you succeeded?
With our carefully considered actions, everything has worked out well so far. Eight years ago, I had an accident myself, but I got off lightly.
What role does the team play on the cable?
You have to be able to rely on your colleagues. Consequently I am pleased that we have an experienced crew. At the moment, we have 10 to 15 men, including three or four head technicians. We all work conscientiously and responsibly; we know that people’s lives depend on our work.
So quality assurance is a guiding principle?
We have to guarantee the safety of our installed cables, roofs and bridges. This involves is a great deal of personal responsibility. When it comes to tensioning, for example, not everything is standardised and we often have to assess the situation for ourselves. This is where the most experience is needed. If I have any concerns, I get the engineers from INAUEN-SCHÄTTI to check again for safety.
What else is involved in a good installation?
Obviously preparation, and close cooperation with the customer. Generally, the project manager and I meet customers on site weeks before the installation, to get to know them, to assign the support staff and to draw up an installation concept. Many things are managed in advance at this time. Then we organise the tools ourselves; we put the crates together individually for each job. That can often take several days. Sometimes the tools can fill two articulated lorries. That’s where cable car cable installation is different from kitchen fitting (he laughs).