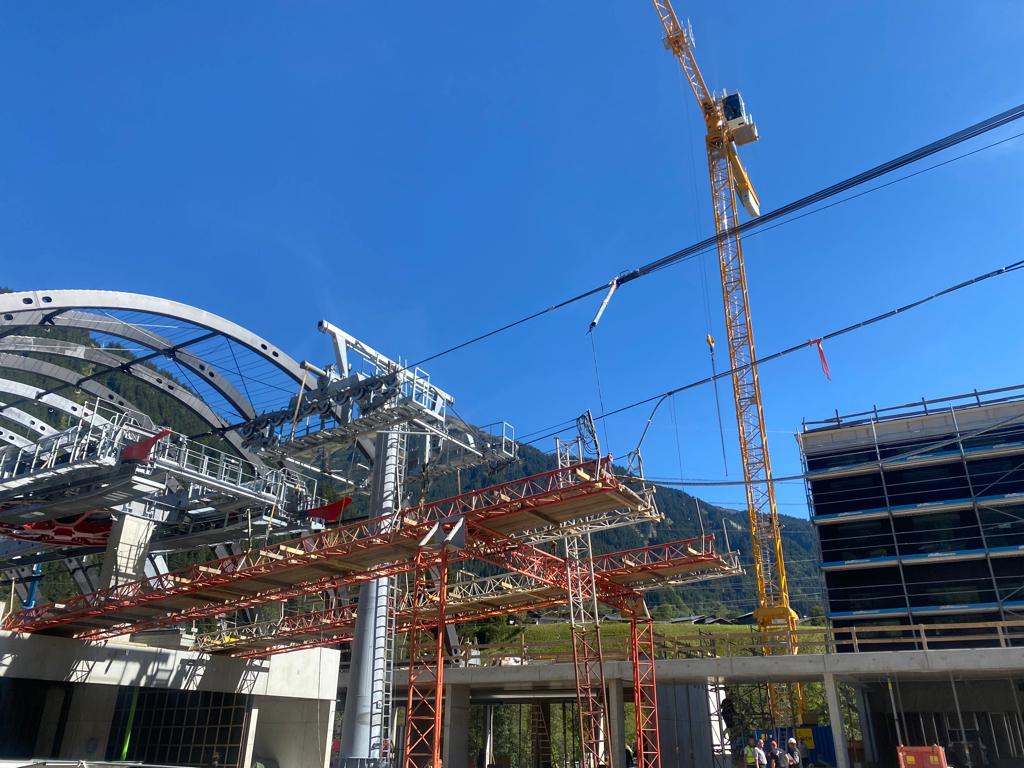
Cableway & Technology
Fatzer’s TRUsplice ES
For several years, cable manufacturer FATZER has been researching the shortened long splice together with Lucerne University of Applied Sciences and Arts as well as ropeway manufacturer DOPPELMAYR/GARAVENTA.
The trials in Silvretta Montafon demonstrate once again that the technology works – despite deviation from the norm.
If a wire rope is supplied for a cable car, there is a problem – or rather there are two problems: the ends. Initially, they need to be interconnected on site, such that a safe, regular, continuous rope is created.
This craft is called splicing, and a long splice is the point at which the rope ends are merged together.
The splices on the haul rope really are long: 60 or more metres, depending on the rope diameter.
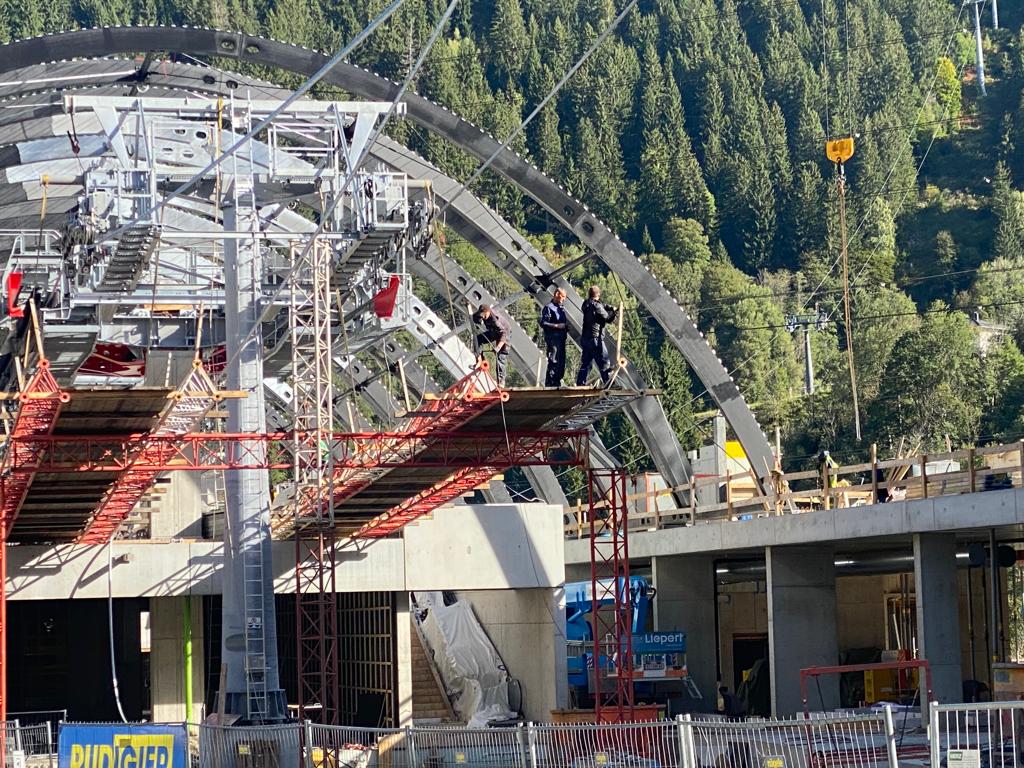
To this day, the basic investigations by Dr. Hans Overlach at Karlsruhe Technical University and their publication in 1931 represent the only scientific work on the transmission of forces in splice joints for cable car ropes.
At that time, hemp was used as an auxiliary material for splicing; today, a special rubber band is used. Although the proven formula has been in use for decades, practitioners in the industry have long suspected that safety would be guaranteed even with a shorter long splice.
FATZER, GARAVENTA and Lucerne University therefore joined forces in 2015 for scientific investigation of the possibility of the short long splice. The title: TRUsplice ES!
The problem of the long long splice
What exactly would be the benefit of a shorter long splice? In a nutshell, installation would be cheaper and easier.
“The rope must be joined in a flat place that is suitable for splicing,” Lucerne University lecturer Prof. René Bärtsch explains.
Yet it is often difficult to find 60 metres of flat ground, especially in the places where cable cars are needed.
The advantages of the short long splice
If the long splice can now be shortened, there is a chance in many places that there will be no need for any scaffolding, as 30 metres of flat ground are easier to find than 60, especially in cities.
Even where scaffolding is needed, the length is reduced by half. That also shortens the installation time. Furthermore, fewer staff are needed to hold the rope when splicing.
On average, the number of support staff needed is reduced by a third, and even emergency solutions or road closures become unnecessary. Instead, splicing work becomes possiblein stations.
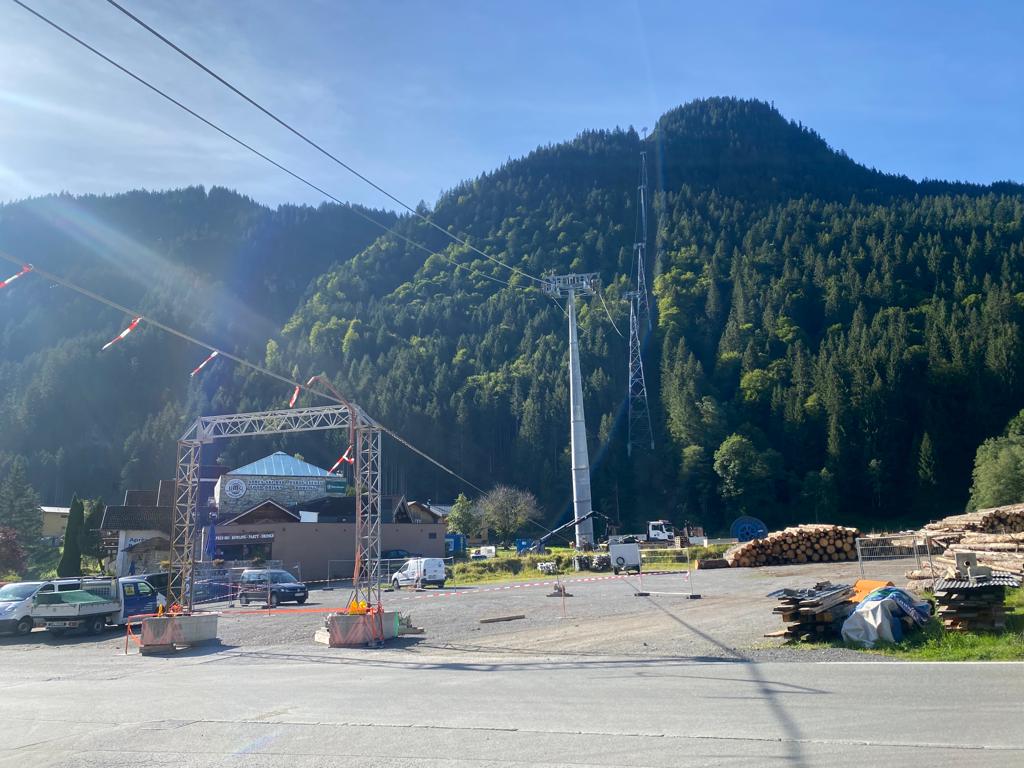
Phase 1: The practice on the test cable car
The starting point for the project was the practical experience of FATZER: for a long time, the development team had already been using shorter splices on the internal test cable car at the wire rope factory in Romanshorn.
After all, a rope that consists solely of splice, owing to the number of test areas, is hardly feasible.
“Even then, we observed that falling below the mandatory splice length of 1,200 x rope diameter is possible with no problem,” Christof Nater from research and development at FATZER reports.
Phase 2: Theory work & test laboratory
To obtain scientifically reliable results from personal experience, FATZER joined forces with Lucerne University.
The experts at Lucerne University set to work on closer examination of the flow of forces within the splice, using mechanics and mathematics, and thus laid the foundations for a new calculation.
Next, the formulae were simulated by computer, and then the watchword was: test, test, test.
“For the basic research, the university designed a globally unique system, which simulates a deflecting sheave. It was produced by GARAVENTA and stands in our factory,” Nater says.
For nearly a year the system was optimised and then various splice lengths, rope diameters and other variations were tested. The finding: the flow of forces in the rope does not behave in a linear manner – as indicated by the norm – but rather initially increases and then decreases.
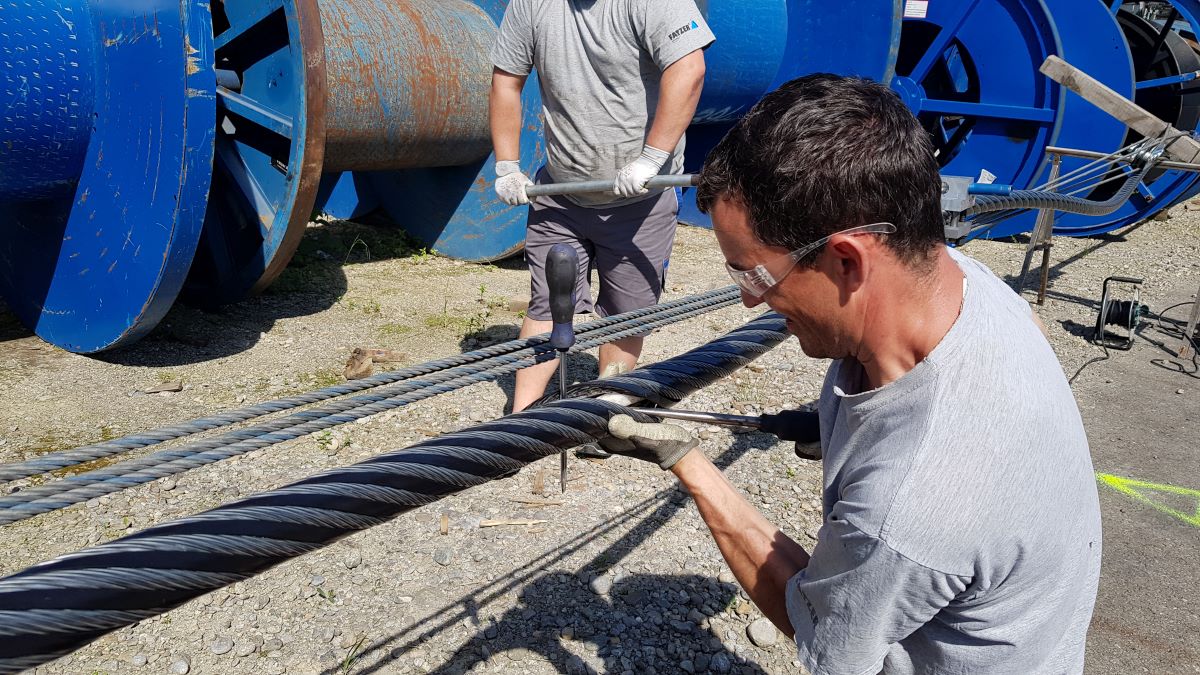
Phase 3: Safety tests in the factory
After the basic research, the investigation returned to the test cable car in the FATZER plant. The experts tested three different splices and demonstrated that, from 480 x diameter, additional length no longer represents additional safety.
Phase 4: Practical trial in Switzerland
With these test results, a short long splice was used for the first time on the Vals-Gadenstatt cable car – with the approval of the federal department of transport.
“We knew that a splice with a length of 480 x rope diameter holds safely. However, to avoid any doubt whatsoever, we then made the length 584 x rope diameter,” Bärtsch says.
The long splice in use undergoes regular visual inspection and is also checked internally by means of a so-called magnetoinductive measuring method, with positive results: the splice behaves as predicted.
Phase 5: Practical trial in Austria
Since 2021 the shortened long splice has also been in use in Austria. Ski resort Silvretta Montafon is using the TRUsplice ES in two new systems: for both sections of the Valisera gondola lift.
The initial results from the still ongoing test series correspond to the previous findings – the advantages are convincing (see quote box). Furthermore, a short long splice is in use on the Madloch chairlift in the ski resort of Zürs.
Phase 6: Certification
At the moment, FATZER is striving to certify the short long splice in the established module H. The project, which has been ongoing for decades, will then have reached a further milestone.
With material from Lucerne University. Author: Senta van de Weetering
Wolfgang Rudigier
Operations Manager of Valisera cable cars I & II in the ski resort of Silvretta Montafon
“In the case of the long splice, it is high time for something to change; the standard is outdated. I was therefore very pleased when FATZER approached us in 2021. With AURO autonomous operation, the new Valisera cable car is already technically innovative; now we are moving up another level with the short long splice. The splice in the bottom station, directly on the circulating sheave, has many advantages: short splice bridges, less material, lower costs, shorter working time and a lower staffing requirement. The safety of the short long splice is tried and tested: the rope behaves no differently from a long-spliced rope.”