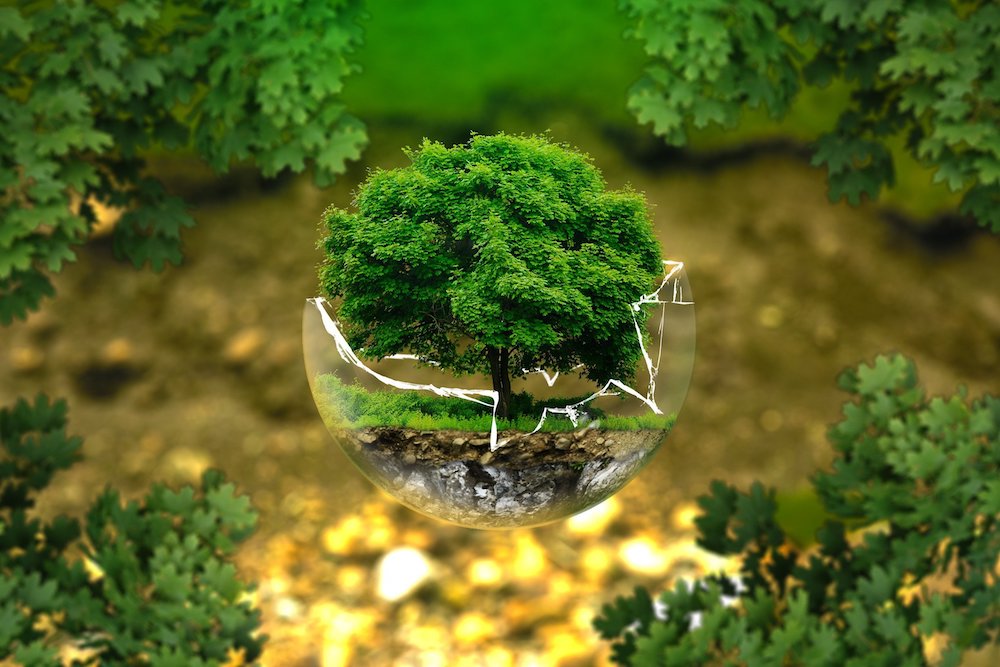
SI 2/2023, Wartung & Service
Interflon: Wartung und Instandhaltung reloaded
Die Daten sind unglaublich und stammen aus der Studie von Kenneth Holmberg und Ali Erdemir mit dem Titel “Influence of tribology on global energy consumption, costs and emissions” (2017): 20 Prozent des weltweiten Energieverbrauchs werden zur Überwindung von Reibung aufgewendet.
Das sind unfassbare 103 EJ (Exajoule). Weitere 3 Prozent (16 EJ) werden dazu verwendet, um verschlissene bzw. kaputte Teile nachzuproduzieren und zu ersetzen. Auch wenn ein Teil dieses „Reibungsaufwands“ Autoantriebe ausmachen, geht ein großer Teil auf das Konto der Industrie.
Die beiden Autoren führen weiter aus, dass mit innovativen Technologien um 1.460 Mt weniger CO2-Emissionen (langfristig sogar bis zu 3.140 Mt!) verursacht würden. Das entspräche einem Einsparungspotential von 450.000 Mio. bis 970.000 Mio. Euro.
Mangelhafte Schmierung
verursacht 15 bis 40 Prozent der Instandhaltungskosten. Grafiken: INTERFLON
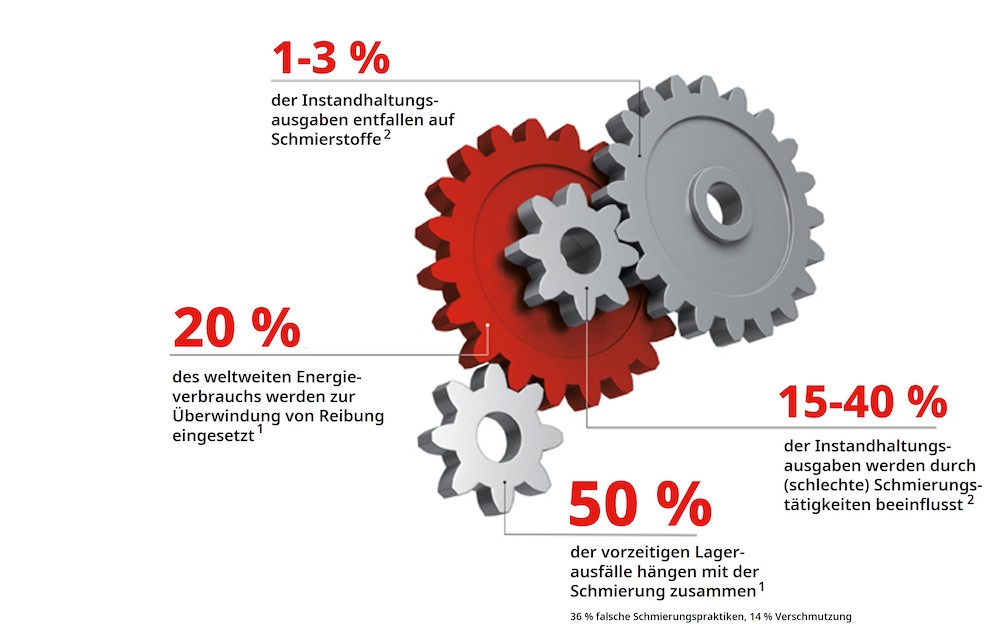
Wartung verlängert Maschinenleben
Was kann man nun aber konkret im eigenen Unternehmen zur Reduzierung von Energie und Kosten tun? Eine gute Schmierung reduziert nicht nur die Reibung und damit den Energieaufwand, sondern verlängert auch das Leben der einzelnen Maschinenkomponenten von Seilbahnanlagen und anderen zu wartenden Geräten.
Immerhin liegen 15 bis 40 Prozent der Instandhaltungsausgaben laut SKF in einer mangelhaften Schmierung begründet. Dabei handelt es sich um Wartungsstunden, die verursacht werden, um Lagerschäden wieder zu beheben.
50 Prozent aller Lagerschäden sind demzufolge durch inkorrekte oder unzureichende Schmierung verursacht. Damit Reibung reduziert wird, muss eine Maschine oder Anlage richtig funktionieren.
Dazu zählt auch die Verwendung von Komponenten, die auf die Umgebungsbedingungen – etwa Temperatur und Feuchtigkeit – sowie auf die Anforderungen wie Last und Drehzahl optimal abgestimmt sind. Das betrifft sowohl Material-, Oberflächen- als auch Schmierstofftechnologie. Genau da liegt auch das größte Einsparungspotential.
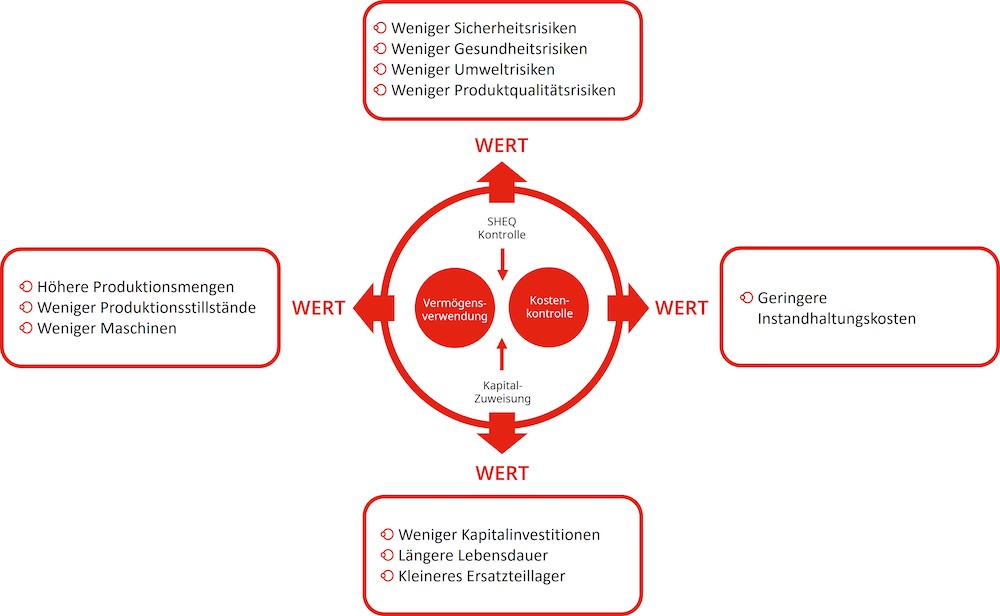
Umdenken erfolgt
Der Ansatz „Wartung kostet nur Geld“ gehört heute zum Glück in vielen Seilbahnunternehmen der Vergangenheit an. Nicht ernst genommene Schmierwartung geht im Endeffekt zu Lasten der Leistung und der Umwelt. Ein neuer Ansatz trägt nicht nur zur CO2-Reduzierung, sondern auch zur Senkung der Kosten und Erhöhung der Leistung bei.
Diesen Umschwung in der Denkweise von Unternehmen weltweit sieht auch Peter Bakkum, Geschäftsführer von INTERFLON HOLLAND:
„Schließlich führt eine unzureichende Wartung der Schmierung zu Produktionsverlusten aufgrund von Stillstand und kürzeren Wartungsintervallen. Letzteres kann wiederum mit der Entwicklung von Wärme und Verschleiß infolge von Reibung zusammenhängen. Zusammenfassend lässt sich sagen, dass wir mit einer guten Schmierstoffwartung die Reibung und damit deren Auswirkungen auf Kosten, Leistung und Klima reduzieren.“
CapEx vs. OpEx
Dieser neuen Trendwende folgend hat sich INTERFLON zur Aufgabe gemacht, die Wartung “weiterzudenken”. Unter dem Motto „Instandhaltung Reloaded“ plant das Unternehmen auch den gesamten Produkt-Lebenszyklus mit ein.
Dazu gehört das Wissen über Tribologie (Einfluss von Materialien, Bewegungen, Kräften und Schmierstoffen aufeinander), das die technischen Berater von INTERFLON ihren Kunden im Zusammenhang mit der kompletten betrieblichen Instandhaltung mit auf den Weg geben. Mit diesem Know-how erkennen Geschäfts- und Produktionsleiter, wie sich Schmierwartung nicht nur auf die jährlichen Betriebskosten (OpEx, Operational Expenses) auswirkt, sondern auch auf die CapEx (Capital Expenses), die einen künftigen Nutzen beschreiben.
Der Einfluss der Schmiertechnologie reicht über den gesamten Lebenszyklus der Produktionslinie hinaus – diese neue Betrachtungsweise setzt sich immer mehr durch und ist richtungsweisend für eine nachhaltige Produktion ganz im Sinne einer Kreislaufwirtschaft.
Längere Wartungsintervalle
INTERFLON-Produkte sind im Gegensatz zu herkömmlichen petrochemischen Schmierstoffen mit effektiven Additiven und MicPol®-Partikel verstärkt. Diese Partikel bilden die sogenannte „Bonding Bridge“, die einen sehr langhaltenden Schmierfilm mit minimaler Reibung ermöglicht.
Auf diese Weise reduzieren diese Schmierstoffe Reibung und Verschleiß viel besser als herkömmliche Produkte, insbesondere unter ungünstigen Bedingungen wie extremen Druckbelastungen, hohen und niedrigen Temperaturen, starker Verschmutzung sowie in nassen oder feuchten Umgebungen.
Die MicPol®-Technologie in Kombination mit Schulungsprogrammen, Beratung, Software und Hardware ermöglicht es Kunden, die höchsten Anforderungen bei den Seilbahnanlagen in Bezug auf Sicherheit, Effizienz und Emissionen zu erfüllen.
Geringere Kosten
Kunden profitieren von einem deutlich reduzierten Schmierstoffverbrauch und Wartungsaufwand. Das verlängert die Lebensdauer der kritischen Komponenten, minimiert Ausfallzeiten, reduziert den Stromverbrauch sowie die CO2-Emissionen. Gleichzeitig verbessert es die Leistung und Zuverlässigkeit der Anlagen.
Somit hilft INTERFLON Unternehmen, ihre Wartungs- und Energiekosten zu senken und gleichzeitig Ausfallzeiten zu reduzieren. Rund 400 qualifizierte technische Berater unterstützen weltweit Kunden vor Ort bei der Optimierung ihrer Prozesse.
Mittels ausgewählter Schmierstoffe werden effektive und kostenreduzierende Lösungen realisiert. INTERFLON bietet Schmierstoffe mit außergewöhnlich guter Leistung zur Wartung von Seilbahnanlagen und aller zu wartenden Maschinen und Geräte wie Pistenraupen, Beschneiungsanlagen oder Sommerrodelbahnen.
INTERFLON-Produkte senken nicht nur Wartungskosten, Energieverbrauch und CO2-Emissionen, sondern verbessern auch die Zuverlässigkeit der Komponenten. Auf der Interalpin in Halle B / 032 präsentierte INTERFLON ihre innovativen Schmierstofflösungen.